Rotating systems
For identification of longitudinal defects
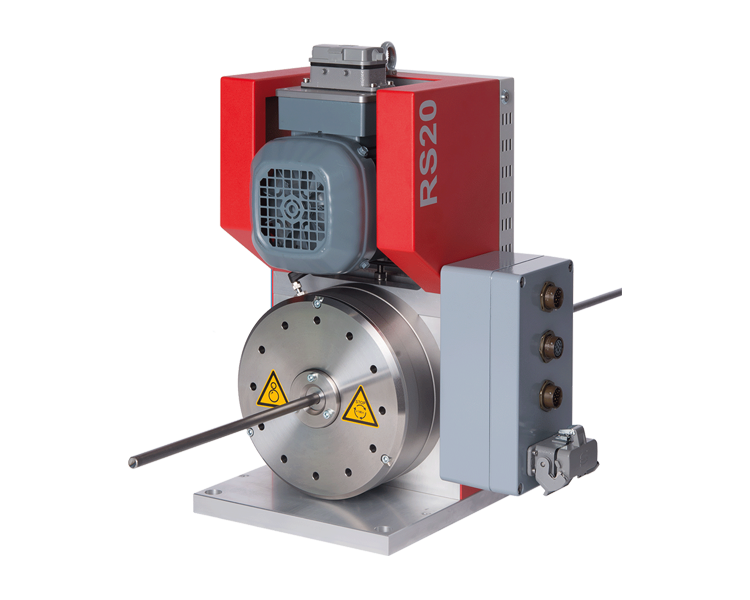
For wire, bars, seamless tubes
Diameters from 1.9 to 140 mm to suit any production line
Material throughput speeds of up to 2880 mm/s can be achieved in wire drawing or recoiling systems
Schedule a free product demo
Please leave us a message and we will contact you to schedule a free product demo at your premises.
Reliable quality assurance for your semi-finished products
- For offline, inline and continuous testing
- Available in four sizes:
– RS20: 2–20 mm (1/16–3/4 in)
– RS35HS: 3–35 mm (1/8–1¼ in)
– RS65: 5–65 mm (3/16–2½ in)
– RS140: 10–140 mm (3/8–5 1/2″) - Electronic lift-off compensation system for optimum signal-to-defect correlation
- Extremely robust design
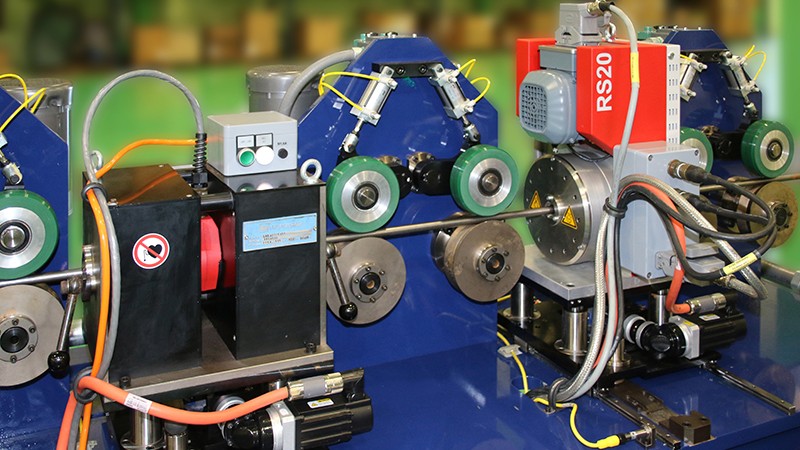
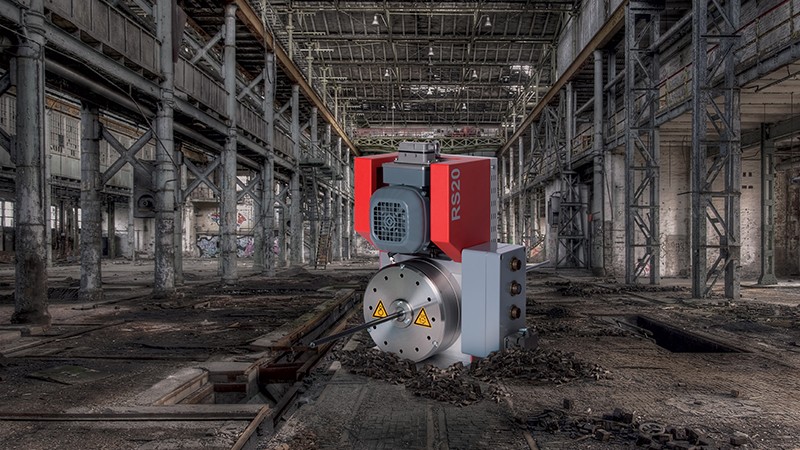
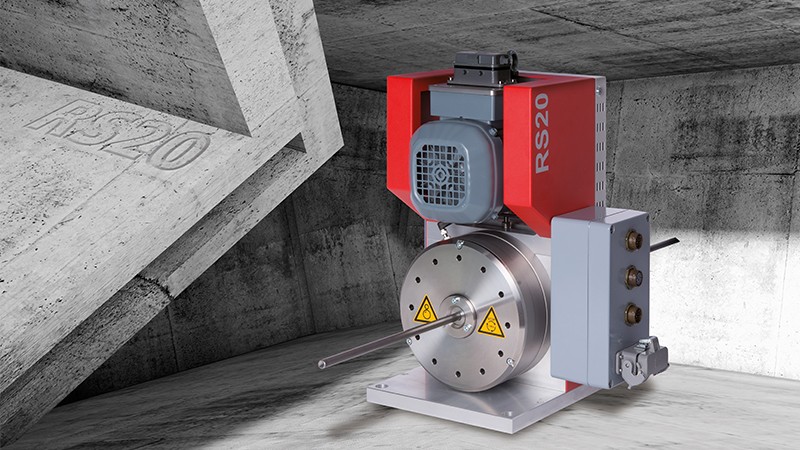
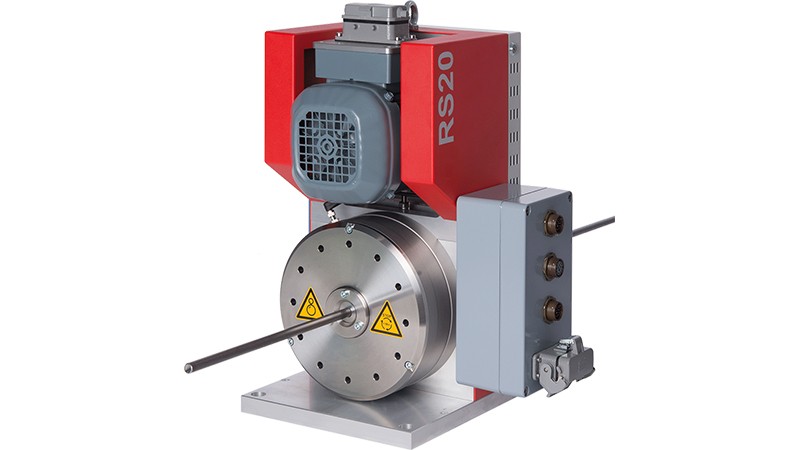
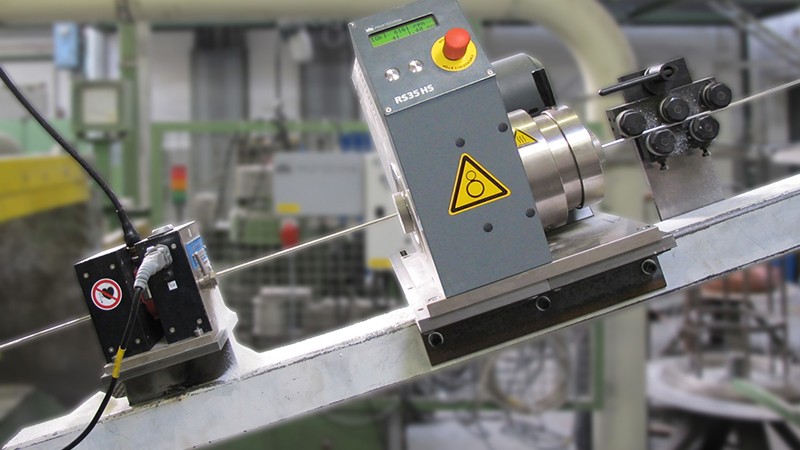
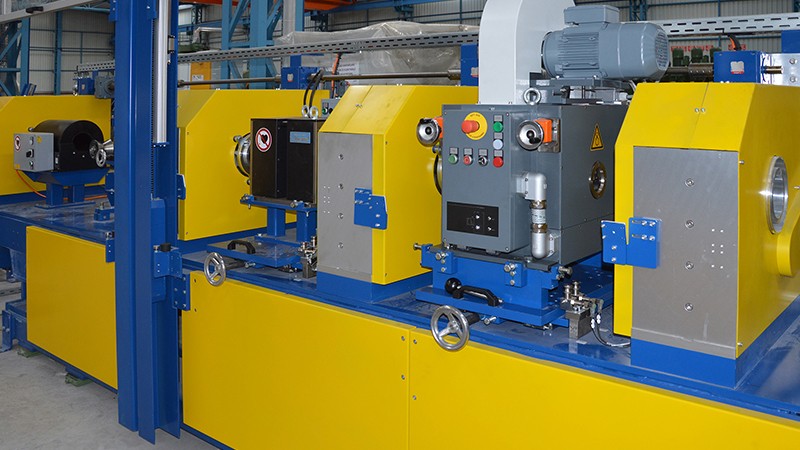
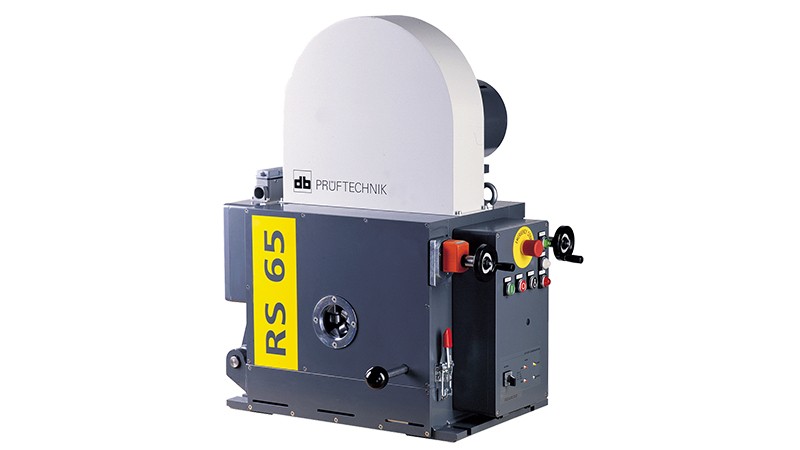
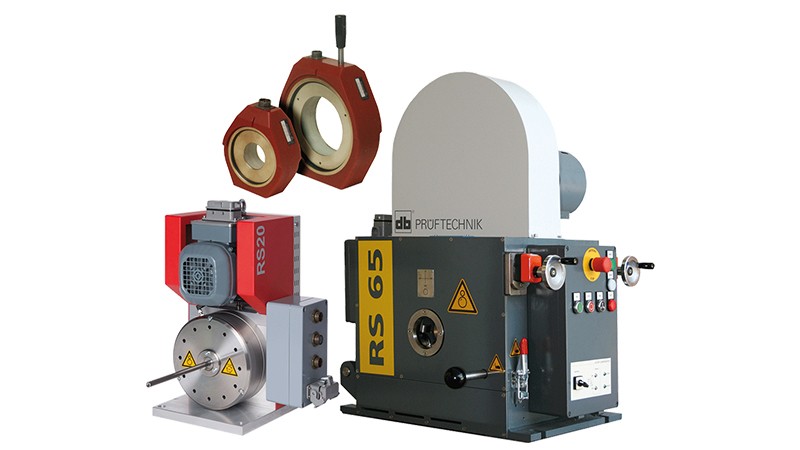
INTERESTED?
Find out more ...
Eddy current testing system with a clever sensor design
- Reliable quality assurance for your semi-finished products with diameters from 2 to 20 mm in terms of longitudinal defect detection
- Minimum conversion times when changing to a different diameter through replacement of the entire sensor disk
- High durability since the sensor has no moving parts
- Ideal for installation in production lines (drawing lines) due to compact design
- High material throughput speed of up to 2.88 m/s with gap-free testing
- Highly precise defect signal output with liftoff compensation system
The RS20 rotating system for the nondestructive eddy current testing of round metallic products such as tubes, rods and wire with diameters from 2 –20 mm achieves high throughput speeds and is ideal for installation in production lines due to its compact and rugged design.
High speed rotating system
- For identification of longitudinal defects in high speed applications
- Diameter range: 3–35 mm (1/8–1¼ in)
- Rotational speeds of 6 000, 9 000 and 12 000 rpm allow high testing speeds
- Inline and offline inspection in applications such as wire drawing, cold heading and spring making
- Rapid diameter adjustment from the outside without opening the device
The RS35HS rotating system has been designed specifically for user-friendly operation. Whether in the setup mode or during testing, there is no need to open the device when changing to a new material. All procedures can be carried out externally, increasing safety and shortening change over times.
The RS35HS is capable of finding longitudinal defects in bar, wire and seamless tubing at very high speeds. Unlike standard coils that move parallel to the defect, the probes in the rotating system spin around the test piece, crossing a longitudinal defect multiple times, thereby delivering a very accurate picture of defect characteristics. The high rotation rate of this system (up to 12 000 rpm) ensures that the surface is scanned completely, even at high speeds. With the precision provided by the lift-off compensation system, which compensates for variations in the gap between the probes and test material, the rotating system represents an extremely reliable method for defect detection.
Testing for longitudinal defects
- For identification of longitudinal defects
- Diameter range: 5–65 mm (3/16–2½ in)
- Lift-off compensation system for optimum signal-to-defect correlation
- Extremely robust design
The RS65 PRUFTECHNIK rotating system finds longitudinal defects on tube, bar or wire fast and reliably. Unlike standard coils that move parallel to the defect, the probes in the rotating system spin around the test piece, crossing a longitudinal defect multiple times, thereby delivering a very accurate picture of defect characteristics.
With the precision provided by the lift-off compensation system, which accounts for variations in the gap between the probes and test material, the rotating system represents a reliable method for defect detection.
Testing for longitudinal defects of large diameters
- For identification of longitudinal defects
- Diameter range : 10–140 mm (3/8–5 1/2″)
- 8 or 4 differential channels on two test probes
- Lift-off compensation system for optimum signal-to-defect correlation
- Extremely robust design with flexible probe arms
PRUFTECHNIK rotating systems find longitudinal defects on tube, bar or wire fast and reliably. Unlike standard coils that move parallel to the defect, the probes in the rotating system spin around the test piece, crossing a longitudinal defect multiple times, thereby delivering a very accurate picture of defect characteristics.
With the precision provided by the lift-off compensation system, which accounts for variations in the gap between the probes and test material, the rotating system represents a reliable method for defect detection